Magnox, Berkeley NPP, UK
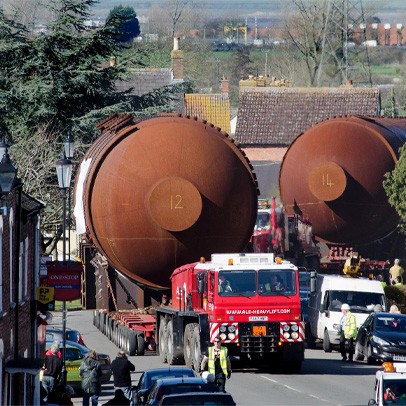
Background
Berkeley had two natural uranium-fuelled Magnox reactors. Each reactor had eight boilers (heat exchangers). One of the boilers was size-reduced on-site and decontaminated by Magnox in 2011. Through Low Level Waste Repository (LLWR) the option of transporting the boilers whole was identified to minimise the risk associated with on-site working option for the 15 boilers remaining in place. Each boiler was ~310 tons in mass, representing a total mass for treatment in excess of 4 650 metric tons.
Cyclife was appointed to carry out a feasibility study for all aspects including stakeholder engagement with regulators, local authorities, local ports and councils in order to underpin the feasibility of shipping from Berkeley to Cyclife Sweden for treatment. 2012 Cyclife was awarded the contracts for lot 1 (x5 boilers) and in 2013 lot 2 (x10 boilers).
Challenge
- Both contracts were against a tight timeline with numerous stakeholders, contractors and regulators from UK and Sweden
- The customer's goal was to achieve a skyline change at the site, maximising the recycling of the metals and minimising the return for expensive disposal of secondary waste supporting their net zero targets and decommissioning plans.
- The stored boilers at Berkley were creating ground loading issues around the reactor buildings impinging on the reactor basement levels and had to be removed without the use of cranes which would have increased the ground loadings.
Our proposal
Key milestones:
- 2012: Transport of x 5 boilers / 2013: Transport of x 10 boilers
- 2014: Completion of treatment and return of secondary waste
Process:
- Design and Characterisation: engineering assessments
- Site Enabling Works: preparation on-site and off-site
- Transport of whole units requiring a complex onsite jacking procedure and multimodal road and sea transport solution for the abnormal-loads. Requiring 3 separate transhipments per boiler via 2 different ports and x2 different sea going vessels before off loading at Cyclife Sweden facility for size reduction of each boiler within our tailor-made large component cutting hall, decontamination, melting and return of secondary waste
Customers benefits
- All the secondary waste generated was suitable for disposal via the LLWR
- ~ 30% of this secondary waste suitable for disposal as LALLW saving valuable space in the LLWR
- No secondary waste was classified as ILW, although initial characterisation identified this to be a project risk, based on the C-14 content
Results
- Over 98% volume reduction as a result
- Recycling of 94%mass of the delivered tonnage within conventional industry